
I tested the ‘pixel’ cut facets with a series of images, but the resulting projected images were disappointing. The size of the top of each of the ‘pixel’ profiles relative to the angle between them (as one profile cut steps down to the next profile cut) was too small. I discussed this with Geoff and we decided to try a few more tests with slightly larger ‘pixel’ sizes. I had designed the original tests to be 1mm square, we decided to increase this to 1.5 mm square and see what happens to the projected image with these profiles. I will post the outcomes these tests are complete.
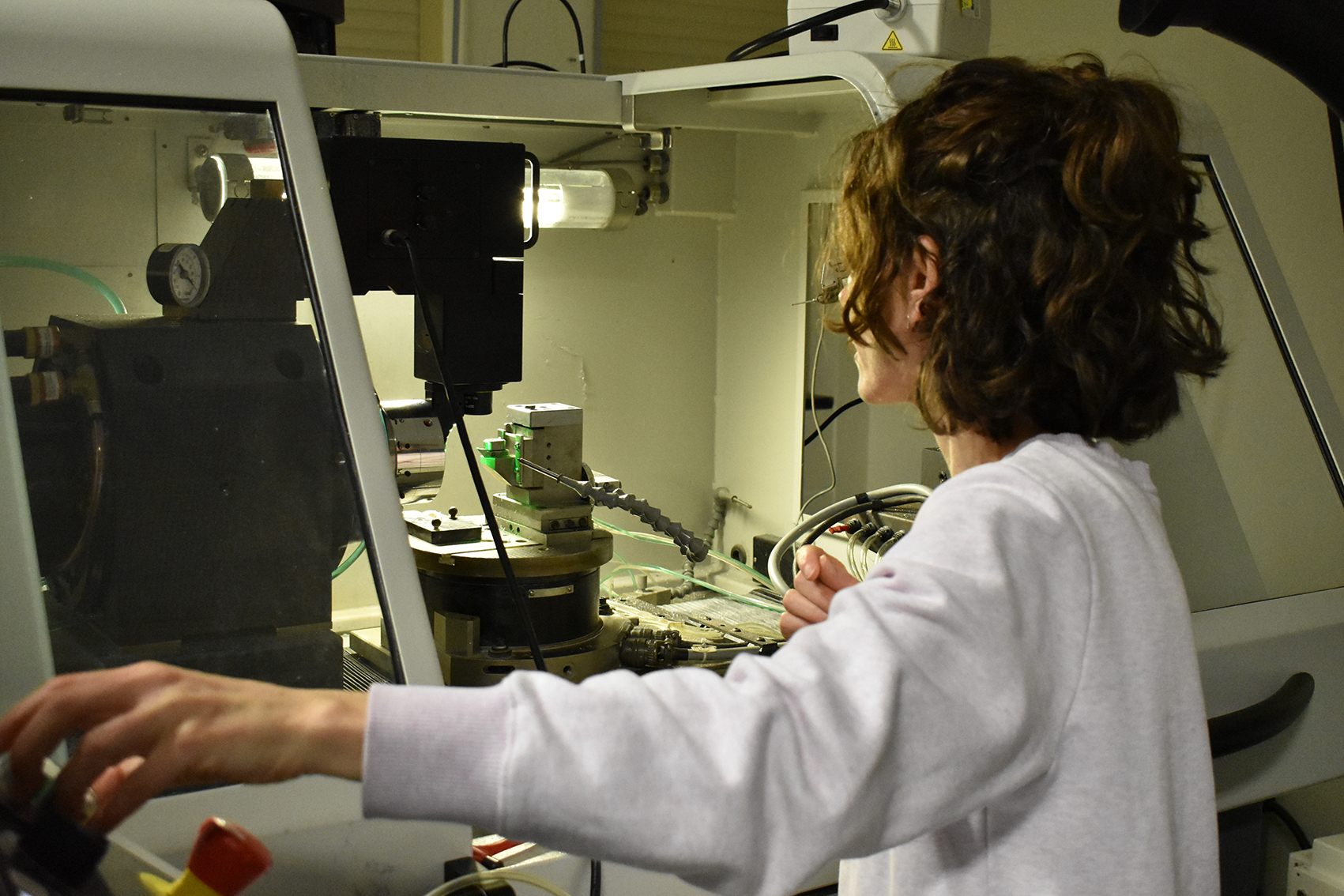
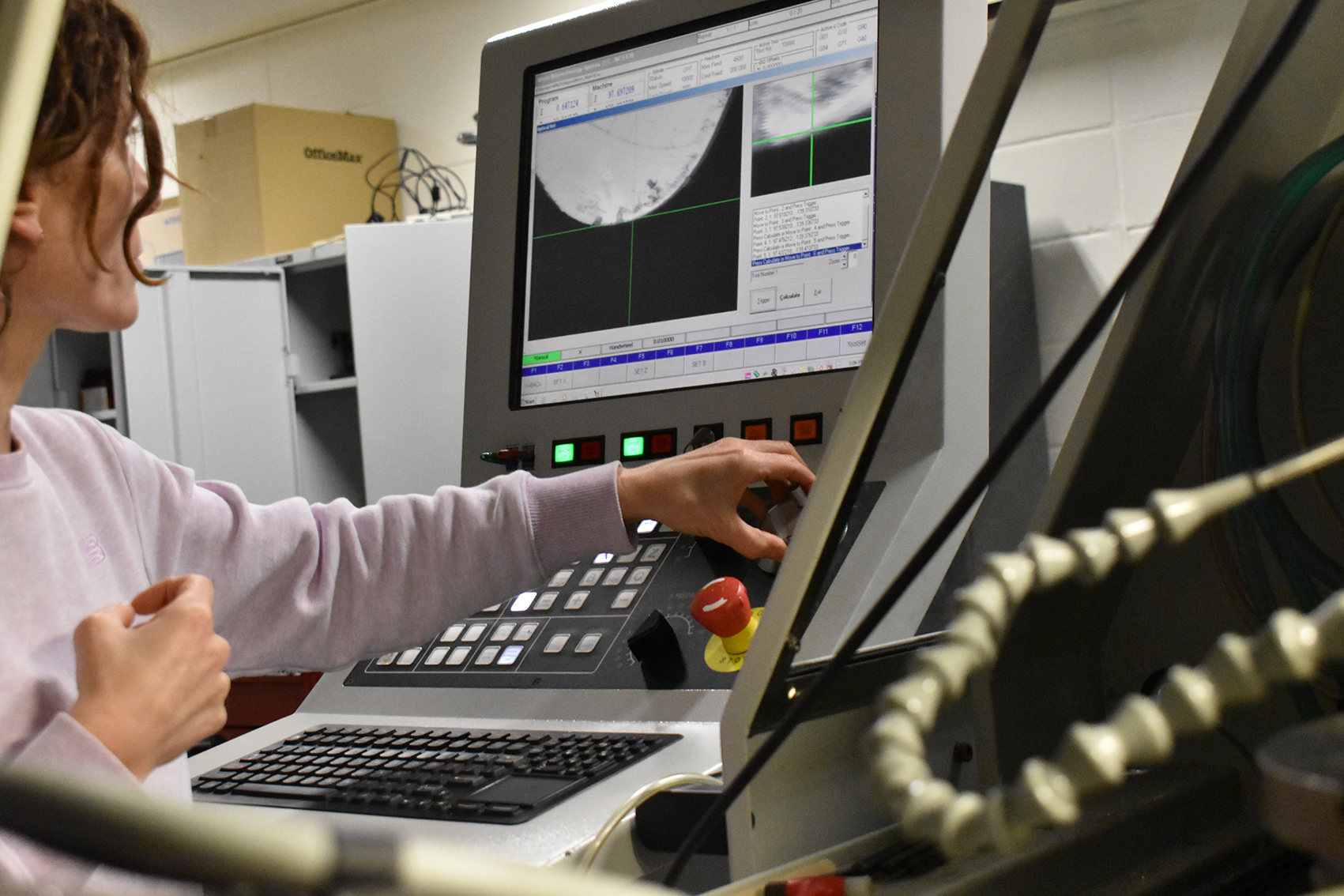
In the meantime I am continuing (as quickly as the nano-lathe allows) with the line cuts. I have developed a more systematic approach in how to cut my facets and am aiming to make as many as I can with the time left on the residency. This has meant making many more facet blanks and I have started a production of facets. Jordan Haddrick from the Maker Space has been helping me with the production run. As introduced in my previous post, we have been making the facets in lots of 3, preparing them on the band saw and lathe and then moving on to the Tormach mill for the profile cutting and finishing.
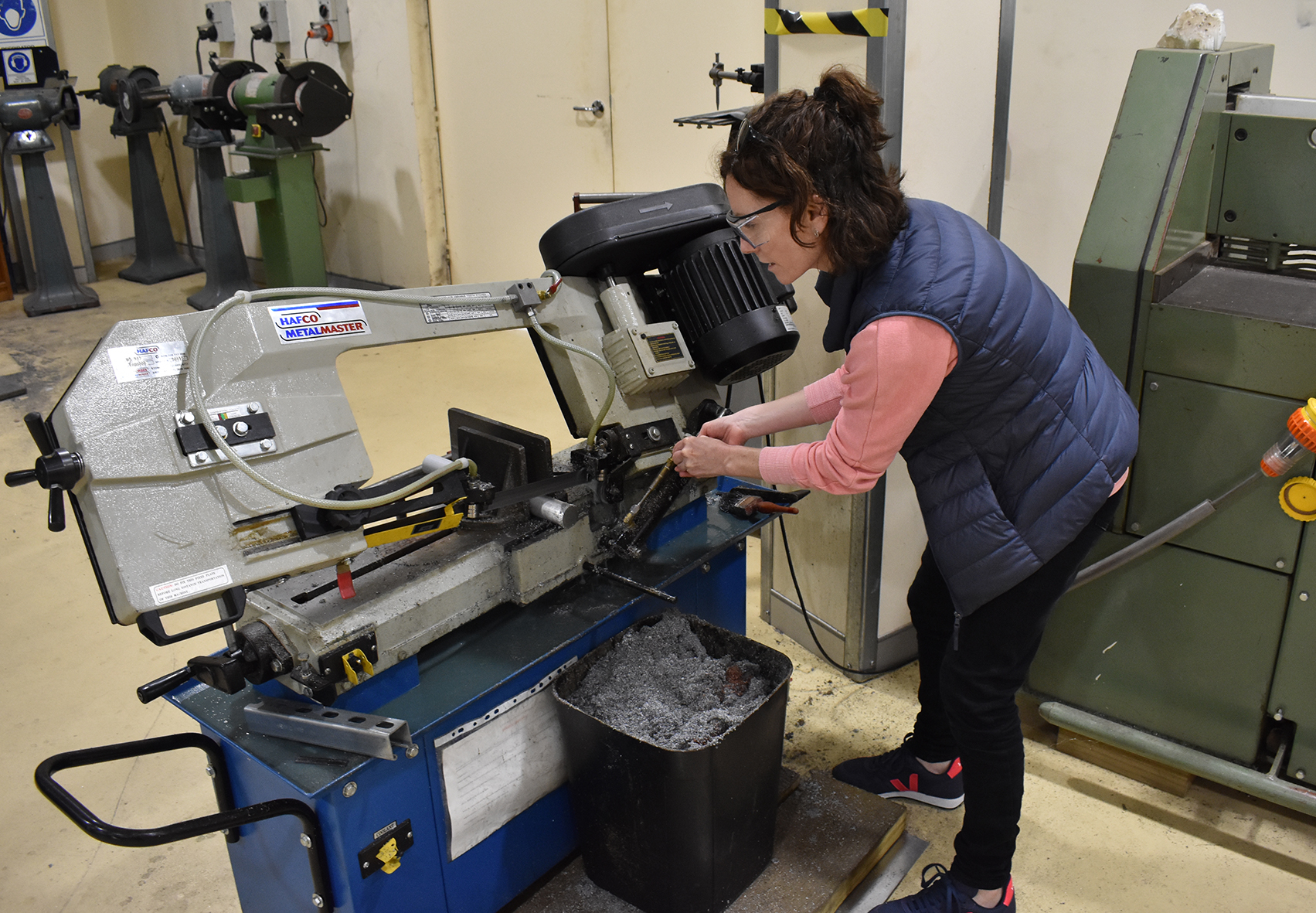
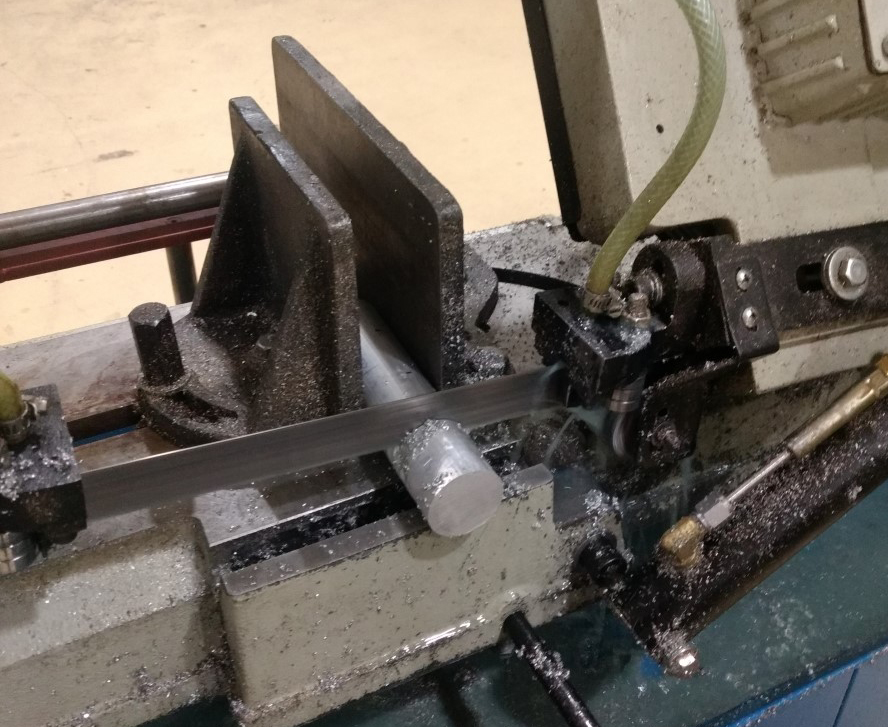
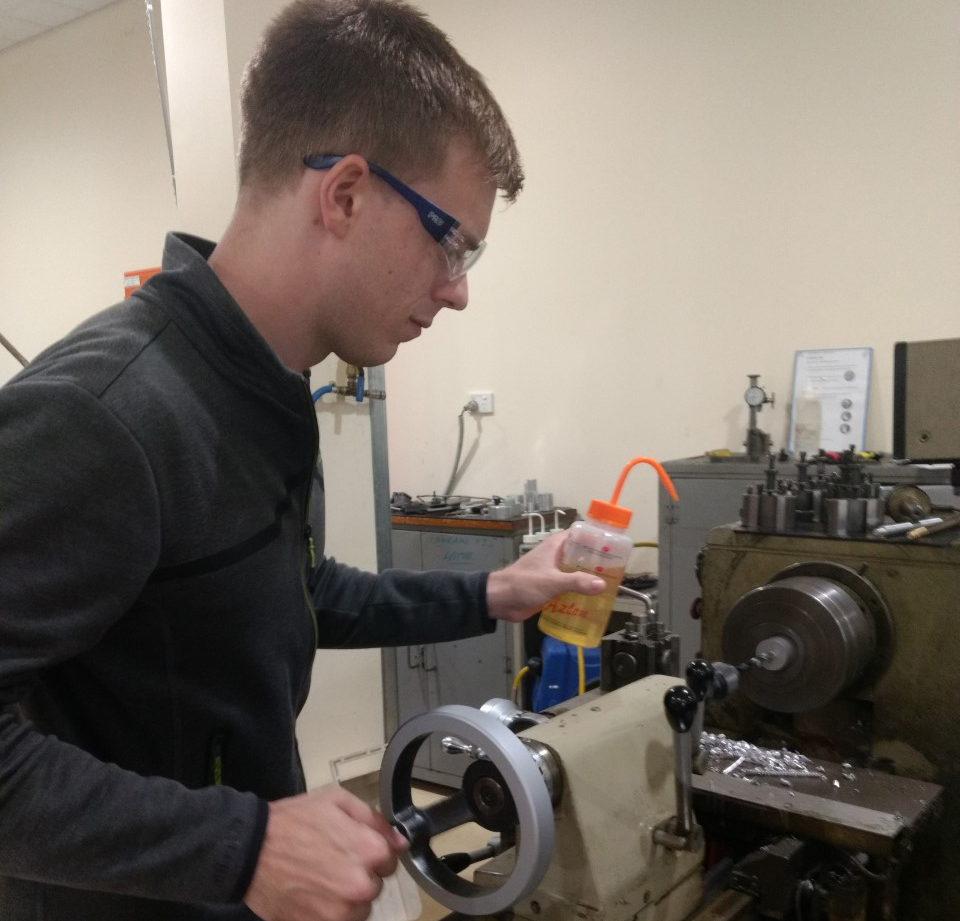
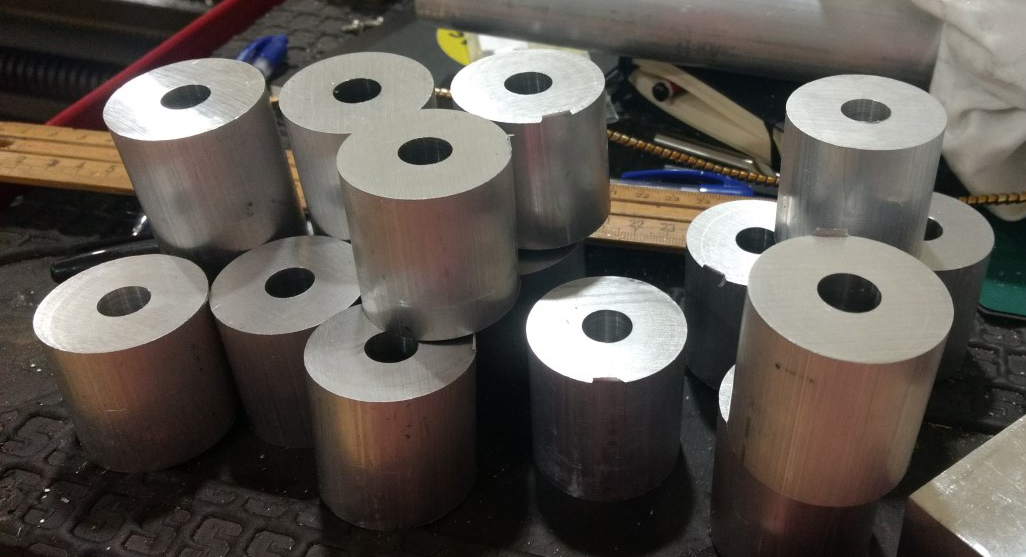
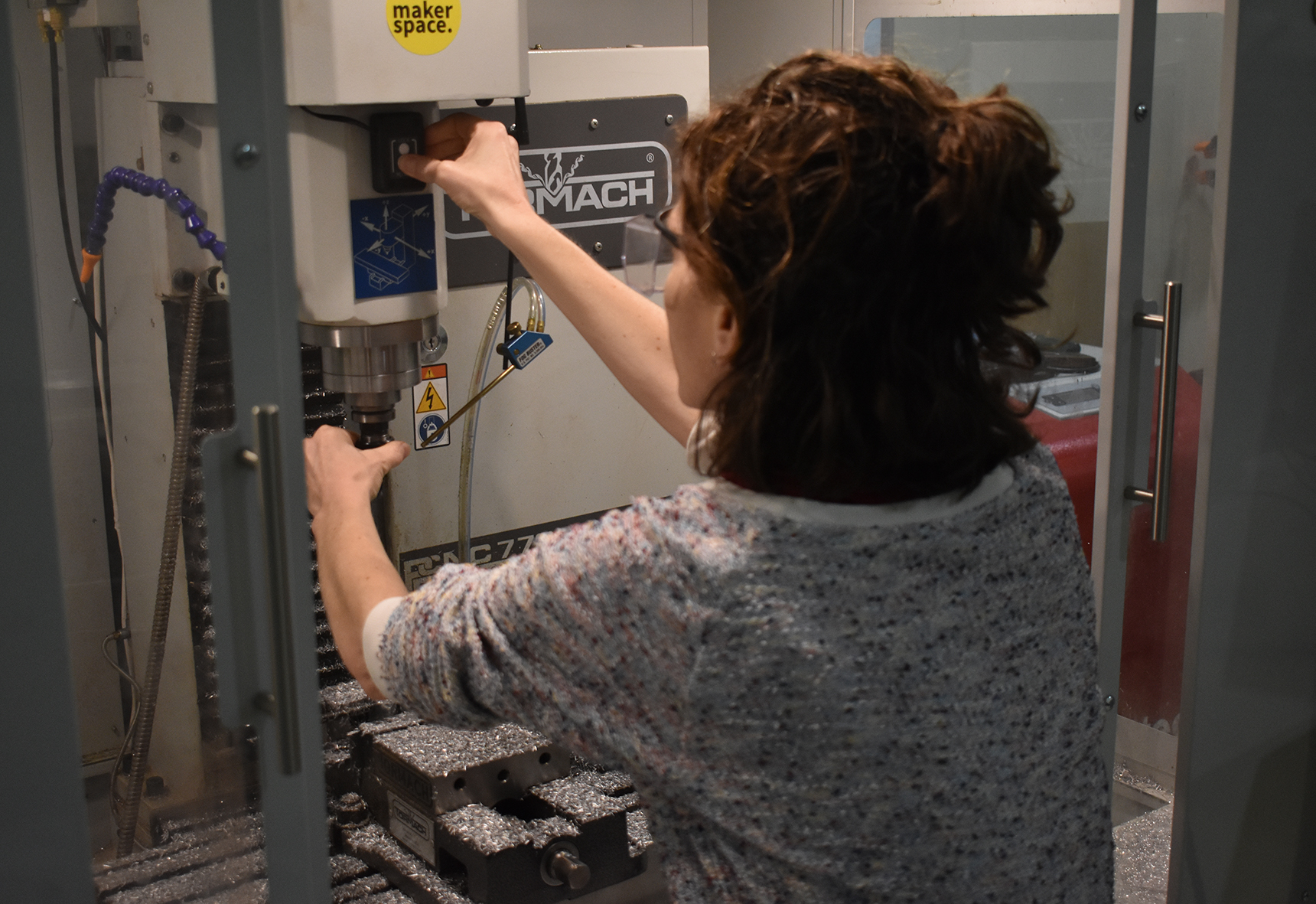

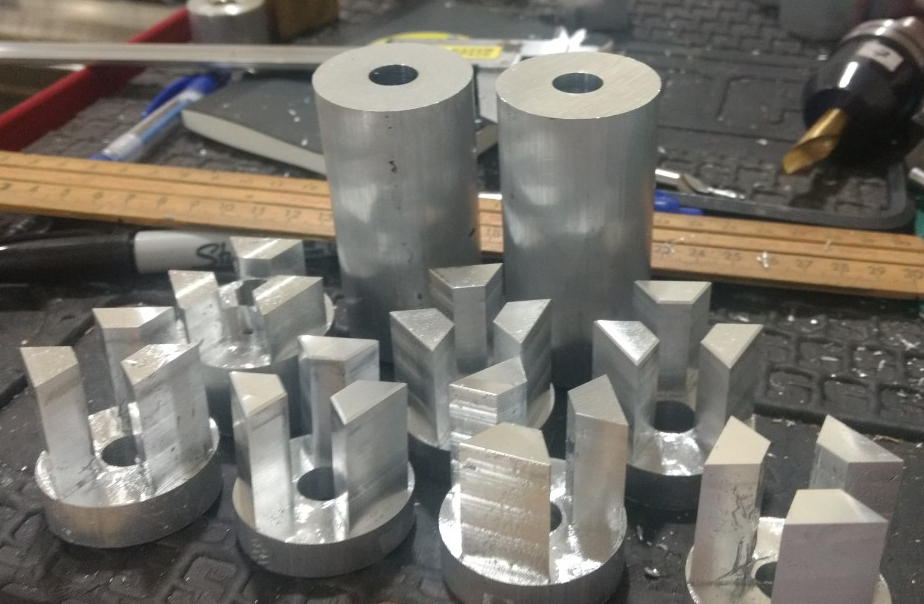